Table of Contents
In industries reliant on shipping and warehousing, effective pallet management can lead to significant cost savings, enhanced efficiency, and reduced product damage. Pallet optimization is more than just loading goods onto pallets; it’s a strategic approach to improve resource utilization, reduce transit risks, and streamline supply chain processes. Lafayette Engineering recognizes the importance of pallet optimization and is committed to helping companies leverage optimized pallet management for improved results.
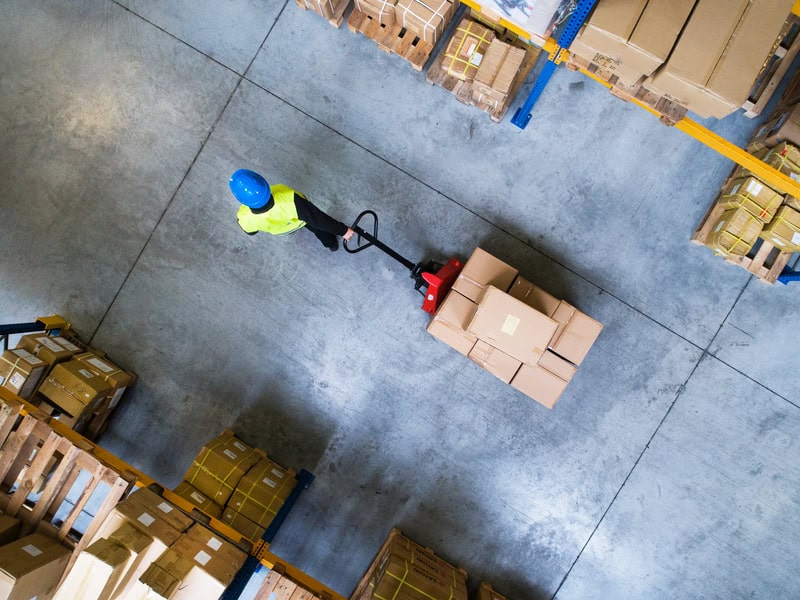
1. Maximizing Packaging Efficiency
Optimizing pallet loads begins with smart packaging choices. Every item should be packaged to maximize space without compromising the security of the goods. This means selecting materials that add minimal weight but offer high durability. Lightweight, strong materials not only make for safer loads but also lower transportation costs since more products can fit on each pallet.
- Why It Matters: Reducing wasted space through optimized packaging enables more units per pallet, directly lowering the cost per unit shipped.
- Best Practices: Companies should consider customizing packaging for popular products to fit efficiently on a standard pallet size. Compression-resistant packaging materials can allow for stacking without risk of crushing.
In some industries, products can be standardized into stackable sizes or dimensions, making it easier to achieve consistent pallet configurations and better space utilization.
2. Selecting the Right Pallet Type for Your Products: Pallet Management
Choosing the appropriate pallet type for specific goods is crucial. The primary pallet types include block, stringer, and solid deck pallets, each with unique benefits. Block pallets, for instance, are generally stronger and can handle heavier loads, while stringer pallets are more lightweight and suited for products that don’t require high durability.
- Material Choices: Wood is the most common pallet material due to its durability and cost-effectiveness, but plastic pallets are ideal for industries that require hygienic and moisture-resistant materials, such as food and pharmaceuticals.
- Customization Options: Some products may need specialty pallets, such as metal pallets for heavy, bulky machinery. These pallets can be costly but prevent damage to both the product and pallet, lowering overall repair and replacement expenses.
For companies that handle diverse goods, investing in multiple pallet types may yield the best long-term benefits, allowing them to tailor pallets to the specific needs of different products.
3. Protecting Pallets and Products from Damage
The integrity of a pallet load can be compromised by several factors during storage and transport, from temperature changes to handling practices. To mitigate these risks, proper protection of the pallet and load is vital. Simple measures like using pallet collars, stretch wrap, and load straps can make a significant difference.
- Importance of Wrapping and Strapping: Stretch wrapping can secure the items on a pallet tightly, preventing shifting or damage during transit. Adding a protective layer, such as bubble wrap or plastic covers, may help reduce damage from environmental exposure.
- Preventative Maintenance: Regularly inspecting pallets and removing damaged ones can prevent costly accidents and ensure that only sound pallets enter circulation. Companies using high-volume storage facilities should implement automated checks or regular inspections.
With robust pallet protection in place, companies experience fewer product losses, reduced returns, and lower costs from product replacements, all of which contribute to a more sustainable operation.
4. Ensuring Optimal Stacking Techniques and Load Configuration
One of the core principles of pallet optimization is efficient stacking and load configuration. By placing products in balanced, secure stacks, businesses can reduce the risk of product shift and collapse.
- Key Stacking Patterns: Using uniform or interlocking stack patterns creates a stable load. Grid patterns are also popular, where products are stacked to distribute weight evenly across the pallet.
- Weight Distribution Tips: Heavier items should always be placed on the bottom layers to stabilize the stack. Overhang should be avoided at all costs, as this can lead to damage to the pallet itself or the products on it. Overhangs can also lead to higher costs if products are damaged and require returns.
Efficient stacking isn’t just about protecting products; it’s about making the most of the space available. With intelligent configuration, businesses can increase the number of items on a pallet without exceeding weight limits, leading to better space utilization and lower transportation costs.
5. Implementing Automation to Enhance Consistency and Efficiency
Automation in pallet optimization brings a level of precision and repeatability that manual methods can’t match. Automated palletizing systems can configure loads based on product dimensions, weight, and stacking requirements, ensuring that each pallet is consistent and efficient.
- Benefits of Automation: Automation reduces the risk of human error, increases speed, and ensures consistency in pallet stacking. This is particularly useful for companies with high shipping volumes or seasonal demand spikes.
- Types of Automation Systems: There are different automation technologies, from simple conveyor systems to advanced robotic palletizers that can adjust stack configurations on the fly. Automated wrapping systems can also be beneficial, ensuring that every pallet is consistently wrapped without requiring manual labor.
For companies looking to streamline their operations, automated systems provide a long-term investment that pays dividends in productivity and efficiency gains.
The Role of Lafayette Engineering in Optimizing Pallet Management
Lafayette Engineering is a trusted provider of customized material handling solutions, including pallet optimization systems. Our services range from assessing current pallet usage and recommending solutions to implementing fully automated palletizing systems that meet your specific industry needs.
By working with Lafayette Engineering, companies can access the latest in pallet optimization technology and strategies tailored to their products and logistical requirements. We prioritize creating efficient, cost-effective solutions that enhance operations and reduce waste, benefiting both the bottom line and environmental impact.
Conclusion
Pallet management optimization is a cornerstone of efficient logistics, impacting everything from shipping costs to product safety. By implementing these five essential rules, companies can enjoy a streamlined supply chain that enhances productivity and cost-efficiency. Whether you’re looking to adopt better packaging practices, invest in automation, or select the right pallets for your products, Lafayette Engineering can help. Contact us today to explore customized pallet optimization solutions designed to transform your business operations.
Frequently Asked Questions (FAQs): Pallet Management
1. What types of pallets are best for heavy products?
- Block pallets are generally recommended for heavy products because of their structural integrity and ability to support large loads.
2. How does automated pallet optimization improve efficiency?
- Automated systems provide precise stacking and wrapping, reducing human error and increasing the speed and consistency of pallet handling.
3. What is the best way to prevent pallet damage during shipping?
- Using protective wraps and securing products with strapping or pallet collars can minimize damage during transit, keeping loads intact.
4. How can Lafayette Engineering help with pallet optimization?
- Lafayette Engineering offers tailored pallet optimization solutions, including consulting, pallet selection guidance, and automation integration for enhanced efficiency and reduced costs.
5. Are there environmental benefits to pallet optimization?
- Yes, optimizing pallet loads reduces the number of trips needed for shipping, lowering fuel consumption and emissions, and reducing overall waste from damaged products.