Table of Contents
Conveyor control systems are integral to modern material handling, enabling efficient, safe, and precise movement of goods across various industries. These systems encompass a range of technologies, from simple motor controls to sophisticated automation solutions, all designed to optimize conveyor operations.
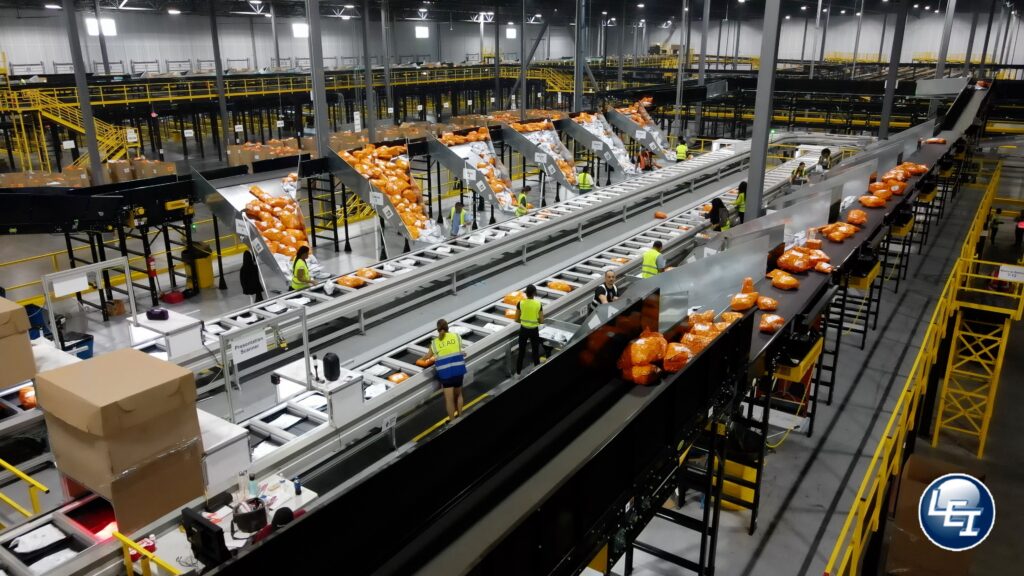
Key Components of Conveyor Control Systems
- Programmable Logic Controllers (PLCs): PLCs are industrial computers that monitor inputs and outputs, making logic-based decisions for automated processes. In conveyor systems, they manage motor speeds, track product positions, and control sorting mechanisms. PLCs offer flexibility and can be reprogrammed to accommodate changes in the production line. Taylor Made Housing Counseling
- Human-Machine Interfaces (HMIs): HMIs provide operators with a visual interface to monitor and control conveyor operations. They display real-time data, system statuses, and alerts, facilitating prompt decision-making and system adjustments. Taylor Made Housing Counseling
- Variable Frequency Drives (VFDs): VFDs control the speed and torque of electric motors by varying input frequency and voltage. In conveyor systems, they enable smooth acceleration and deceleration, reducing mechanical stress and enhancing energy efficiency. Control
- Sensors and Actuators: Sensors detect the presence, position, and speed of items on the conveyor, providing critical data to the control system. Actuators execute movements such as diverting, stopping, or sorting items based on sensor inputs, ensuring precise handling. Control
Integration and Automation
Integrating conveyor control systems with other automated equipment and higher-level management systems enhances overall operational efficiency:
- System Integration: Combining conveyors with automated guided vehicles (AGVs), robotic arms, and other machinery creates a cohesive material handling ecosystem. This integration ensures seamless product flow and reduces manual intervention. MMCI Automation
- Warehouse Control Systems (WCS): A WCS acts as a real-time coordinator for material handling within a warehouse, directing activities and ensuring efficient operation of subsystems like conveyors. It interfaces with warehouse management systems (WMS) to execute tasks such as order fulfillment and inventory management. Wikipedia
Benefits of Advanced Conveyor Control Systems
- Increased Throughput: Automated control systems streamline material flow, significantly boosting processing speeds and handling larger volumes of goods. Lafayette Engineering
- Enhanced Flexibility: Modern control systems can be easily programmed to accommodate different product types, varying production schedules, and future expansion plans. Lafayette Engineering
- Improved Safety: Advanced controls integrate with safety sensors to detect potential hazards like jams or misaligned products, triggering immediate shutdowns to prevent accidents. Lafayette Engineering
- Reduced Downtime: Diagnostic tools within control systems monitor vital parameters like motor temperature and belt tension, alerting operators to potential issues and allowing for preventative maintenance. Lafayette Engineering
Considerations for Implementation
When implementing or upgrading conveyor control systems, consider the following:
- Scalability: Choose systems that can grow with your operational needs, accommodating future expansions or modifications.
- Compatibility: Ensure new control systems can integrate seamlessly with existing equipment and software to maintain operational continuity.
- User Training: Provide comprehensive training for operators and maintenance personnel to maximize the benefits of the control system and ensure safe operation.
In conclusion, conveyor control systems are vital for optimizing material handling operations. By leveraging advanced technologies and integrating them into broader automation frameworks, businesses can achieve significant improvements in efficiency, safety, and adaptability.
Innovations in Conveyor Systems Revolutionize Material Handling
Japan is revolutionizing logistics with a groundbreaking 310-mile-long conveyor belt system designed to transport shipping containers automatically, replacing the need for approximately 25,000 trucks. This innovative system enhances efficiency, reduces carbon emissions, and addresses labor shortages in the transportation sector. By integrating advanced conveyor control technology, the project showcases how automation can transform supply chain operations on a massive scale.